Transformers have a coil of insulated wires which work as current-carrying conductors around the core. These coils are one of the key parts in a transformer and are mostly made of either aluminum or copper. Both aluminum and copper are conductive metals and have their own pros and cons with regards to their use in high voltage transformer winding. One needs to consider their application requirements when choosing the right metal for transformer core and windings. There are a few other factors one needs to consider before making a decision. This post discusses a comparative account of which one serves better as a high voltage coil winding.
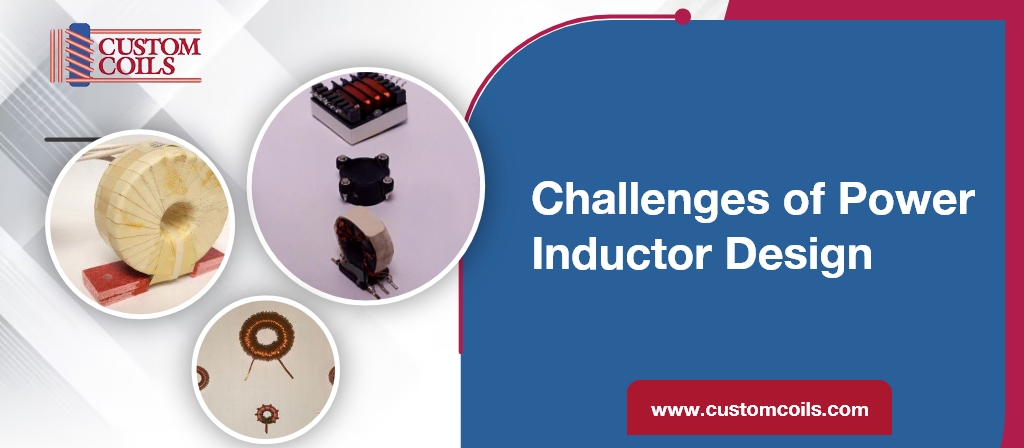
Pros and Cons of Aluminum as a High Voltage Coil Winding
Here are some pros and cons of aluminum as a high voltage transformer winding metal.
Pros
- The heat generated in the circuit is stored in the windings. When it comes to heat per pound storage, aluminum has a better capacity than copper.
- Aluminum is lightweight and hence does not add to the weight of the transformer. This reduces density and is especially useful in power distribution segment.
- Aluminum is cost effective and hence a budget option for large transformers.
- Aluminum helps reduce eddy currents and shorting possibilities.
- Since it is highly malleable, it conforms to the winding shape easily, which reduces mechanical stress.
Cons
- While aluminum is lightweight, it requires more number of windings and hence may not be suitable in compact spaces.
- While aluminum is resistant to corrosion and moisture, copper is better than the former. Aluminum may require additional layers of coating, which will increase the density of the coil wire.
- Aluminum oxidizes quickly with continuous exposure to air, and hence additional preventive measures and maintenance may be required.
Pros and Cons of Copper as a High Voltage Coil Winding
Here are some pros and cons of copper as a high voltage transformer winding metal.
Pros
- Copper offers better mechanical strength and structural stability to the transformer than aluminum. These transformers are especially used in heavy-duty environments as copper can better withstand mechanical stress and vibrations.
- Copper offers better electrical conductivity than aluminum, which implies it can carry current efficiently and without resistive losses.
- While copper may be denser than aluminum, it has a thinner wire size. Hence, a smaller number of windings are required in case of copper-based transformers. This makes them suitable in compact spaces.
- Copper is easy to weld and fabricate, and also requires less maintenance.
- Copper has a high thermal conductivity and hence is suitable for high heat applications.
Cons
- Copper is more expensive than aluminum. Also, its prices may fluctuate based on market conditions.
- While aluminum oxidizes when exposed to air, it can be insulated. However, when copper starts oxidizing, the parts covered from air exposure also oxidize. So while copper still has better resistance to oxidation than aluminum, once this happens, the transformer may need a replacement.
- The density of copper is high which may add to the weight of the transformer.
Overall, copper is suitable for large transformers and applications where a large amount of heat is generated, while aluminum is better for low to medium heat applications. This also depends on the budget, space available among other factors. So, one needs to decide after weighing all these factors against your application requirements. It is a good option to connect with a reliable transformer manufacturer and discuss your requirements with them. They will do an in-depth analysis and offer you the right answer regarding the type of transformer you need. If you are a part of the energy sector or an OEM of electrical or electronic devices, you will require good-quality transformers. Partnering with custom coils to manufacture your power generation, power transmission, or other power transformer needs is a great sourcing strategy. With regards to custom transformer windings, it is essential to partner with an experienced and reliable manufacturer of transformers. Ensure they understand your requirements and have customization capabilities. Custom Coils is a well-known manufacturer of premium quality high voltage transformers and inductors. The company offers custom coil winding after analyzing your requirements. For any further information, you can contact their team today via phone or email.